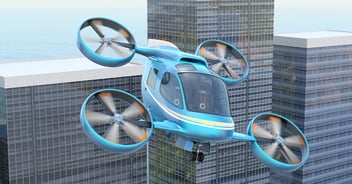
Barcoding in Maintenance : Coding for Better Productivity
Published :
Aircraft maintenance by the very nature of its complex execution process produces a series of records that provide important information about the actual maintenance process being carried out, the state of the aircraft, its various systems and components at various stages of execution and the actual task or activity that is currently being executed. This information needs to be processed, analyzed and interpreted to fully realize and improve operational, budgeting and forecasting efficiencies.
The execution of aircraft maintenance work or maintenance services demands that documents such as engineering orders, work orders, work packages, non-routine jobs etc. be created at a planning level and then issued to execution level. The execution level supervisors then receive, read, and assign these documents to a Mechanic or engineer, and records the assignment details. Shift-In-Charges/Supervisors mostly record this information offline at the end of shift or at the end of each maintenance or service work, since their main goal is to complete the aircraft maintenance task at hand, and adhere to OTP requirements. Therefore, captured data on the time spent completing certain maintenance tasks mostly are only estimations rounded up and based on the each person’s experience, and may not exactly be the actual time taken by the mechanic who performed it. This means that the recorded data are not as reliable as they should be. When there is no access to reliable data, the man-hours and cost used in the maintenance process estimations becomes unrealistic variables and in long run will likely contribute to erroneous estimates, budgeting and cost.
However, a well-designed and implemented bar code system can solve these issues and speed up maintenance processes, particularly those activities that need to be recorded. The system through pre-defined bar code interactions can create a record of all the service-related data: like Work assignment data, Material Requirements etc. Furthermore, with the clock on – clock off actions and hold activity codes, the system automatically records the actual time it takes to perform the work, from beginning to end, recording every action in real-time.
Another requirement in aircraft maintenance is the need to track various aircraft components both because of their operational and commercial importance. With part reliability being in vogue and regulatory requirements such as “Back to Birth Traceability”, etc. a bar code (or some other type of encoding, such as QR Codes or data matrix) assigned to a component easily allows tracking and recording at every stage of its repair work. The component can then be tracked right from its removal from the aircraft, to its movement through the shop or repair process (be it external or internal) and subsequent reinstallation. The bar code marking allows the system to easily maintain a link between the actual/physical component and all its “soft” details in the application. This allows the system to easily locate the component anywhere in the application space, keep track record of the type of repair work that was already performed/being performed and provide a readily available maintenance history.
Bar codes can also be assigned to rotational and consumable materials, as well as for tools before they are distributed to stations, warehouses, or maintenance bases. The system will associate this barcode to the part throughout the organization level and can contain information about its description, manufacturer/repair shop, and for tools that need calibration, the date of its last and next calibration. The system can then be used to control the usage, collect utilization data and subsequent forecasting and planning.
The other, more obvious function that the system can perform is that bar coding can be used to dispatch or receive material in the execution warehouse. Bar coding the dispatch and receiving orders allows easy reconciliation, enabling real time optimization of stock levels and cycle counting of inventory, making the life of material planners and store inspectors easy.
Without a direct record process in Aviation Suite, all of these situations would involve a great amount of documentation, vouchers, signatures, etc. Barcodes provide these types of records and allows more production in each man-hour used in the operation.
Ramco Aviation Solution leverages bar code technology to perform seamless user logins, execute pre-defined tasks and launch the application screens effortlessly. With barcodes included in the work package, mechanics can record the day to day actions that are part of daily maintenance work package processing like Task Clock-On time, Parts Replacement, Material Request, Mark Hold/Wait times, Mark Actual Task/Activity start (Review Task), Task Clock-Off Time and Work Completion by simply scanning the barcodes. These barcodes not only improve productivity of the maintenance personnel by cutting down the time spent on system but also ensures data accuracy. This leads to better utilization of maintenance personnel’s time, resulting in increased production efficiencies and cost savings.
A bar code system may not solve every problem in Aviation maintenance, but it would definitely allow easy and accurate recording of information. This Information accuracy coupled with the automation efficiencies inbuilt in to the data collection processes would result in meaningful and quantifiable process improvements that can increase man power and process efficiencies allowing maintenance personnel to continue working with high productivity rates and help organizations optimize cost.
Vinod is a seasoned Aviation/Aircraft Engineering Industry expert with 11+ years experience in handling and managing multiple cross-functional aviation projects across various airline clients around the world. He has also extensively worked in Process and Project Consultation Activities, Solution Design and Blueprinting and New business opportunity scoping like carrying out Due-Diligence / Requirement Gathering, Business Process Mapping and Analysis, Process Optimization, Process Feasibility Study, Work Scoping, Process Transition, Onsite/Offshore Implementation etc.
All Rights Reserved. © Copyright 2024. Ramco Systems.